기계가공과 3D 프린팅 사이의 ‘해답’, 분말야금 기술
분말야금 기술은 짧은 시간 내에 대량의 제품을 얻을 수 있는 기술이다. 작업자는 분말야금 부품을 통해 더 복잡한 설계를 구현할 수 있다. 또한 절삭 및 가공된 부품의 무게를 덜어낼 수도 있다. 분말야금 공정은 경쟁 기술인 3D 인쇄기술에 비해 더 높은 내구력과 견고성 그리고 품질을 증명하고 있다. 금속분말산업연합은 최근 50주년을 맞은 분말야금 우수설계 경연대회에서 총 14개의 상을 수여했다.
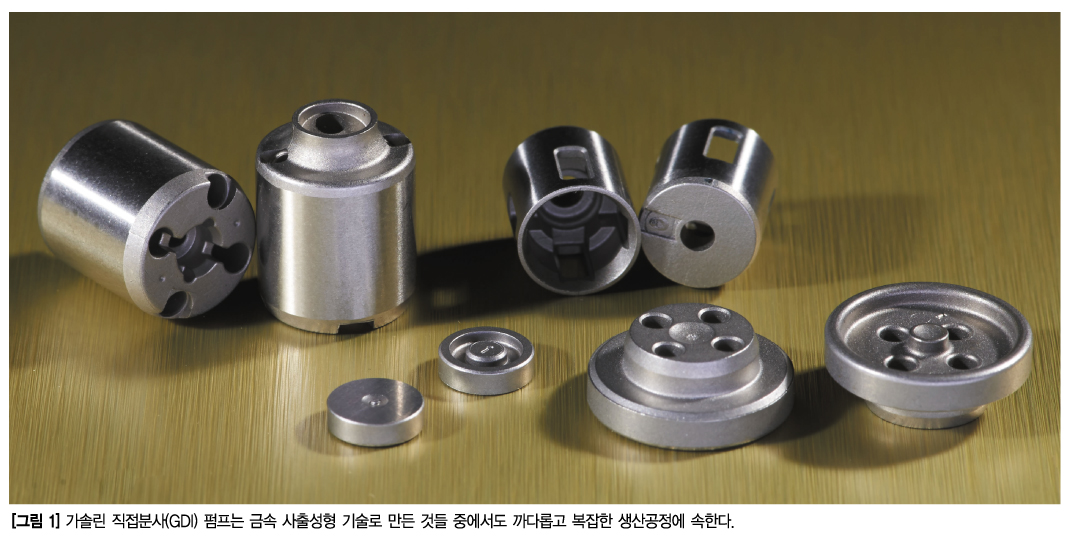
금속 사출성형기술(Metal Injection Molding, MIM)과 압축규화(Press and Sinter) 기술 등을 포함하고 있는 분말야금(Powder Metallurgy, PM) 기술은 자동차 산업을 비롯한 여러 산업분야에서 없어서는 안 되는 기술이다.
분말야금 기술은 대량생산 기계가공(머시닝)보다 월등히 짧은 시간 내에 복잡한 부품 및 제품을 만들어낸다. 짧은 시간 내에 많은 양의 제품을 생산함을 뜻한다.
작업자는 분말야금 부품을 통해 더 복잡한 설계를 만들 수 있다. 또한 절삭 및 가공된 부품의 무게를 덜어낼 수도 있다.
분말야금 공정은 경쟁 기술인 3D 인쇄기술 및 첨삭가공 분야에 비해 더 높은 내구력과 견고성 그리고 품질을 증명하고 있다.
분말야금 제조를 통해 각자 전문분야의 한계를 초월한 회사들을 공식적으로 인정하기 위해, 금속분말산업연합(Metal Powder Industries Federation, MPIF)이 50주년을 맞은 분말야금 우수설계 경연대회에서 총 14개의 상을 수여했다.
2014 분말야금 및 분체 세계대회(2014 World Congress on Power Metallurgy&Particulate Metals)에서 열린 이 대회에서는 총 열네 개의 업체가 수상의 영예를 안았다. 최우수상을 받은 다섯 개의 업체와 아홉 개의 우수상 수상업체가 PM 생산공정에서 각각 선보인 성능 및 비용절감 이점이 화제에 올랐다.
각 부문별 최우수 제품 소개
자동차 엔진 부문
각 부문별 최우수 제품 소개
자동차 엔진 부문
인도 업체인 Indo-US MIM Tec Pvt가 금속 사출성형 조립공정(MIM Assembly) 분야에서 빛을 발함으로써 최우수상을 거머쥐었다. 이 조립공정에서 Indo-US의 제품은 Stanadyne이 만든 가솔린 직접분사(GDI) 펌프의 연료 흐름을 제어한다.
이 공정에는 비어있는 상태에서 기체 배출을 검사하는 장치(Blank Discharge Check), 기체의 흐름을 막는 밸브, 밸브 배출 검사장치, CRV 스프링 시트 등을 포함하고 있다. 앞의 세 부품은 440C 스테인리스강 재질로 이루어졌으며, 마지막 부품은 17-4PH 스테인리스강으로 만들어졌다.
Indo-US MIM 측은 “MIM이 제작한 것들 중 가장 복잡하고 양이 많은 공정”이라고 밝혔다.
이 제품은 기존 제품 대비 35%가량 저렴하며 성능은 더욱 높아졌다. 금속 사출성형기술을 활용하면 구멍의 기하학적 구조를 수정할 수 있다. 이를 통해 흐름에 대한 역학(Flow Dymanics)를 향상시켜 연비를 10~20%가량 높인다.
기체 배출(Blank Discharge) 검사는 이 공정에서 가장 복잡한 부분으로, 각 구멍을 교차시킴으로써 공정을 실현한다. 여섯 개의 측면 코어를 활용한 도구를 사용하는데, 이 중 세 개는 독립적으로 움직인다.
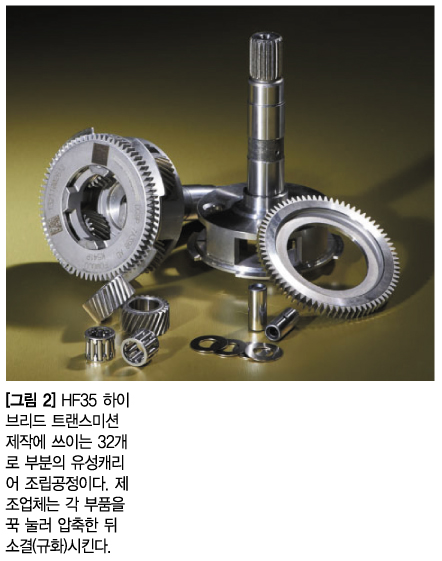
자동차 변속기 부문
키스톤 분말금속(Keystone Powdered Metal)이 유성캐리어 조립공정에서 승리를 거머쥐었다.
키스톤 분말금속(Keystone Powdered Metal)이 유성캐리어 조립공정에서 승리를 거머쥐었다.
포드자동차에 제공되는 32개의 부품조립공정을 통해 링컨 MKZ, 포드 C-MAX, 포드 퓨전 하이브리드 차량에 탑재되는 HF35 하이브리드 트랜스미션을 제작한다. 이는 자동차 트랜스미션에 사용되는 첫 사례다.
키스톤 측은 이러한 공정이 기존 공정 대비 약 25%가량 저렴하다고 추산하고 있다. 이 제품은 생산을 시작한 지 2년 여만에 25만 개 이상이 출하되었으며, 이 중 환불 사례는 단 한 건도 없었다.
샤프트와 연결하기 전에 모판과 스파이더를 꾹 눌러 압축하며, 동시에 규화납땜(Sinter Brazes)을 실시한다. 또한 최대 밀도에 맞추어 헬리컬 피니언 기어를 규화하며 벼린다(Sinter Forge). 기어의 24.5° 각도에 맞추어 장치를 회전하기 위해서다.
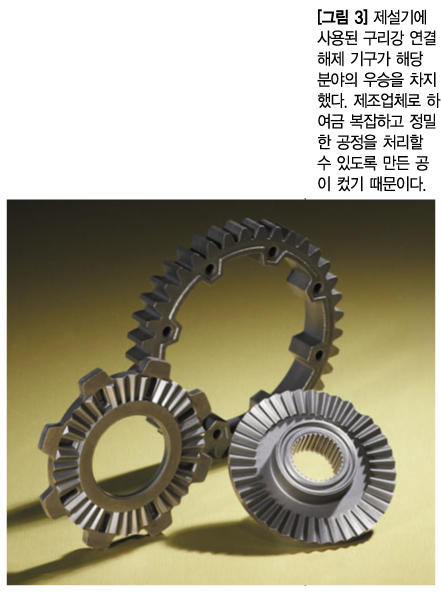
잔디·정원 및 비포장도로(Off-Highway) 부문
캡스턴은 제너럴 트랜스미션사의 제품 제조에 사용되는 구리강 제품을 통해 이 분야에서 기쁨을 누렸다. 각 부품이 모여 제설기 내의 차동 장치 연결을 해제하는 구조를 형성한다. 이로 인해 바퀴와의 연결을 해제함으로써 제자리에서 제설기를 회전시킬 수 있다.
이는 제설기 등의 분야에서는 비교적 최신 기술로, 향후 차동 장치가 급선회 기능이 필요한 유사한 장비에서 새로운 표준이 될 것으로 보인다.
캡스턴은 11개의 압력 단위(Pressing Level)를 자랑하는 두 가지 제품을 만들었다. 일정 시간마다 작동하는 배출기와 정교하고 복잡한 로봇을 통해 펀치로부터 부품을 얻을 수 있다. 또한 부품이 갈라지거나 깨지지 않는다.
복잡한 설계에도 불구하고 제조업체는 이러한 부품들을 정형(Net Shape)으로 형성하고, 특수한 소결기구(Sintering Fixture)가 평탄도 및 단계별 관계를 유지한다.
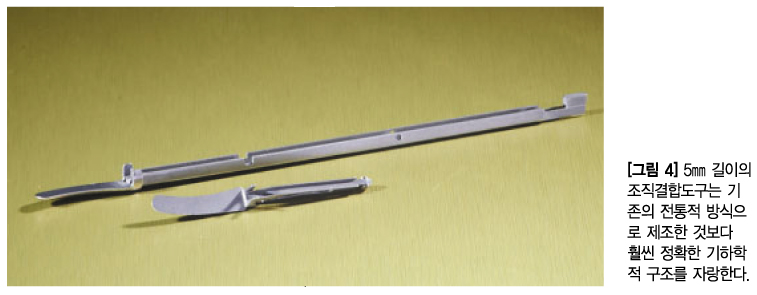
의학 및 치의학 부문
FloMet은 열 조직결합도구 및 해부·조사 도구에 쓰이는 5㎜ 길이의 가지(Tines) 모양 제품을 가지고 이 분야에서 우승했다.
이 제품은 2개의 통 중 1개는 고정되어있고 1개는 이동하는 형식을 취한다. FloMet의 도구와 취합하는 해부·조사 도구는 Altrus라고 하며, ConMed라는 회사에서 만들었다. 열에너지와 압력을 직접 이용해 조직을 밀봉하고 쪼개며 해부하고 응고시킨다.
지금까지 Altrus는 금속 사출성형기술을 탑재하고 있지 않았다. 하지만 현재는 모든 부품에 금속 사출성형기술을 활용하고 있다.
각 부품들은 17-4PH 스테인리스강으로 만들어졌으며, 이전 모델과 비교했을 때 성형 및 가공 분야에 어떠한 제한도 없다. 이 제품에 사용된 금속 사출성형기술은 가지의 길이 및 폭을 정밀하게 고정 및 유지한다. 또한, 가지를 이전 제품보다 더 곧게 만든다.
FloMet 사용자들은 가지의 마감처리에 가열 공정을 활용한다.

전기·전자제품 부문
FloMet은 앞서 설명한 제품 외에도 또 하나의 상을 수상했다. 세 가지로 이루어진 정형화된(Net-Shaped) 오디오 조립공정 부품이 그것이다. 이 부품은 마이크 및 음향장비 제조업체인 슈어가 사용하고 있다.
MIM 기술을 통해 만든 이 제품은 316L 스테인리스강 재질로 만들어졌으며, 분사구 접점, 외부 분사구, 고급 음 분리형 이어폰에 사용되는 금속 이음 고리 등 3가지 부분으로 이루어졌다. 이어폰을 통해 사용자 스스로 주파수 응답 곡선을 조절할 수 있다는 점이 눈에 띈다.
FloMet이 만드는 부품들은 가격이 저렴(이어폰이 지나치게 비싸면 안 되기 때문에)하면서도 깔끔한 외관을 통해 외형적 측면에서도 만족을 주어야 한다. 이 점에서 금속 사출성형기술의 장점이 드러난다.
금속 사출성형기술은 기존 기술보다 더욱 나은 제조를 실현한다. 주물로 만들어진(Die-Cast) 혹은 가공된 부품 없이, 즉 금속 사출성형기술 없이 높은 정밀도를 얻기란 쉽지 않다. 비용마저 줄여야 한다면 더욱 어려운 일이다. 또한 응용사례가 요구하는 자재성능 요구사항을 충족시키는 일 역시 요원하다.
저작권자 © MSD(Motion System Design) 무단전재 및 재배포 금지